The modern and flexible solution. PC-based path control for two to eight servo or stepper motor axes (or for mixed operation), which can be interpolated simultaneously. The standard software includes linear, circular and helical interpolation as well as programming in accordance with DIN 66025 with convenient menu and flexible sub-programme technology. A programme syntax check facilitates programming.
Integrated parameter programming is available for calculating geometrically complex paths. Fixed and freely programmable machining cycles as well as tool management and compensation are also available. All texts and error messages are stored in freely editable ASCII files, making it very easy to adapt to a different language. Customised menus can also be switched to the other language via the language switch in the machine data.
Features |
---|
The standard scope of delivery of the PCCNC includes a 19″ control rack, Windows XP PRO operating system and a powerful user interface. The status display functions in the user interface make it very easy to commission the control system with up to 64 I/O and 16 axis limit switches. The following functions are available for customising the user interface: |
Call up 8 programmes each in manual and automatic mode via function keys. |
Up to 8 additional numerical displays with graphic symbol and value, e.g. for piece counters or processing times. |
Recording of processing parameters via variable pop-up menus |
Display of images (.jpg .bmp ...), e.g. to illustrate menu entries or to guide the operator when loading the machine. |
Basic functions such as homing, limit switch monitoring, manual mode, position lag and in-position monitoring are included in the software. |
The 200-record interpolator buffer can be reloaded during processing. |
Equipment |
---|
Intel/AMD CPU up to 1.8 GHz HDD up to 256GB 2* USB interface 1* RJ45 Ethernet 1* VGA interpolator cycle time 2 msec, position controller cycle time |
200 µsec, high path and position accuracy Speed pre-control for following distance |
Control unit Connection for external rotary encoder or glass scale Analogue interface for connecting a joystick |
Minimisation Up to 64 inputs and outputs in the CNC program Setting and resetting the outputs without stopping the axes Fully automatic tool radius and length compensation Speed-dependent analogue output (option) Speed-dependent pulse output max. 200Hz (option) Continuous movement with all drive types 2*V24 interface: For connecting an external manual control unit |
Technical data (dimensions incl. plug) | |
---|---|
Height | 482 mm (19″ Gehäuse) |
Width | 133 mm (3HE) |
Depth | 350 mm |
Downloads |
---|
Operating instructions and other documents for our control units can be found in the Downloads. |
Have we aroused your interest?
We would be happy to discuss your individual requirements for your project with you.
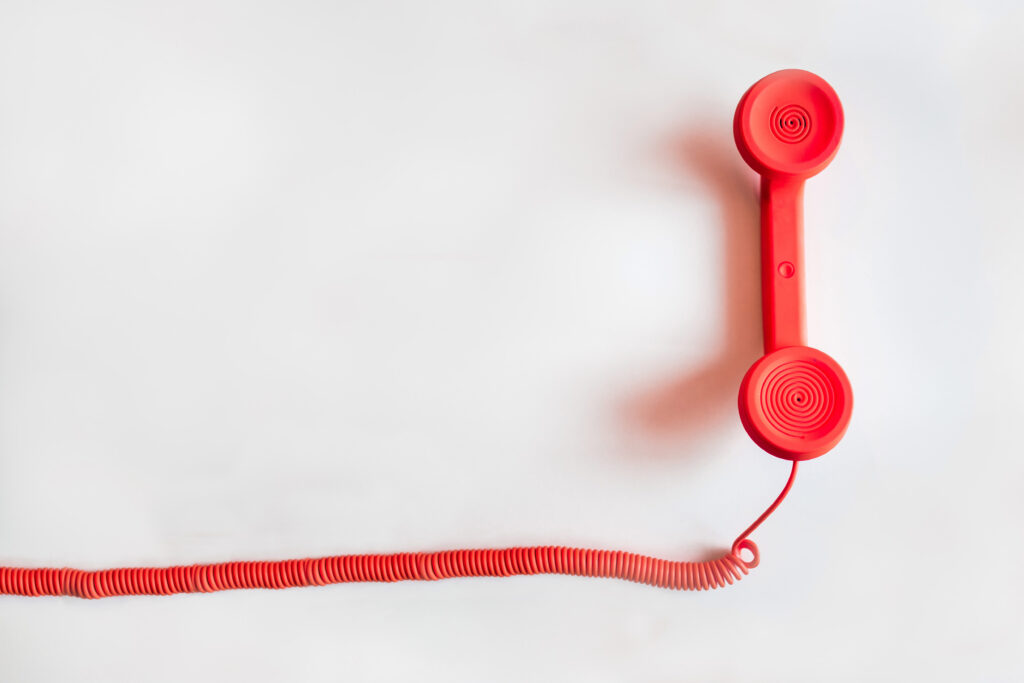